U Included in $28M for cutting-edge tech to clean up iron and steel
April 16, 2024
Above: Zak Fang in his Powder Metallurgy Research lab at the University of Utah
A new infusion of federal funding through the Department of Energy (DOE) totaling $28 million will support some of the most cutting-edge efforts to decarbonize the dirty steel industry, and the University of Utah has received the largest award (~ $3.5 million) of the 13 projects in nine states.
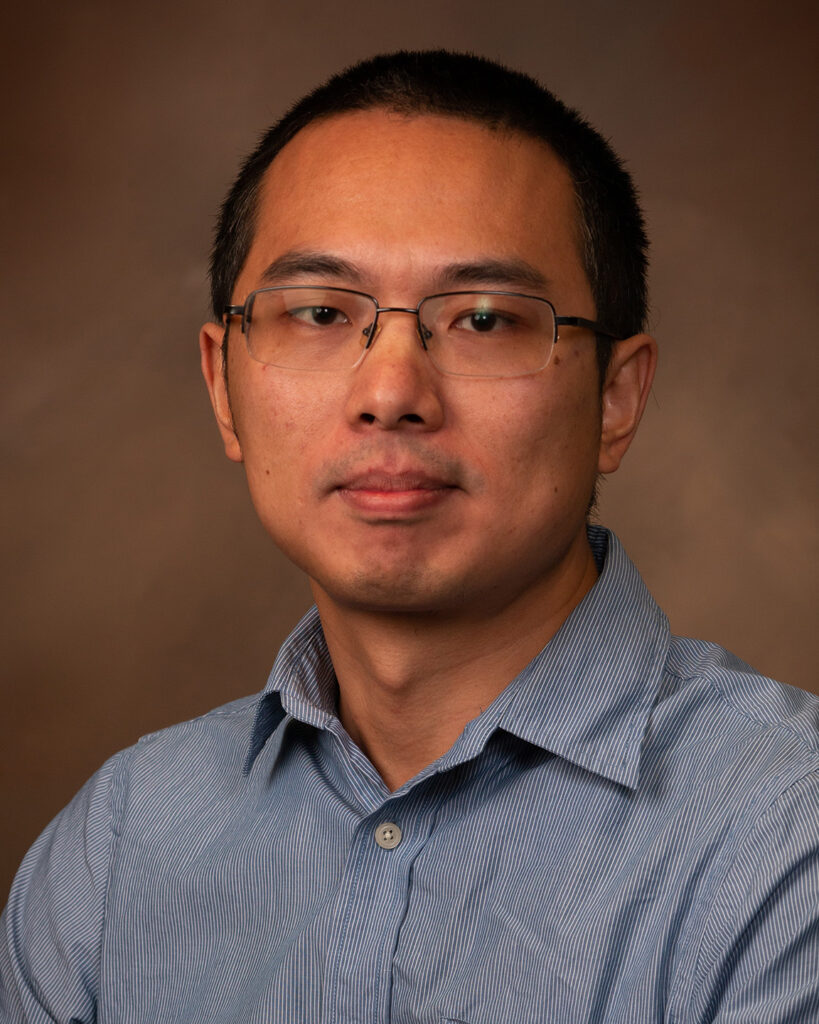
Principal Investigator Pei Sun
The initiative, through the DOE's Advanced Research Projects Agency-Energy (ARPA-E) aims to spur solutions that can eliminate carbon dioxide emissions from the ironmaking process and sharply reduce emissions across the entire steel supply chain, according to an announcement shared with Canary Media, dedicated to news about cleaning up heavy industry.
“Iron and steel production are among the most difficult industrial sectors to decarbonize, which is why ARPA-E is laser-focused on accelerating game-changing technological breakthroughs to lower emissions from these critical sectors,” Evelyn Wang, the agency’s director, said in an emailed statement.
The awards come just weeks after the Biden administration announced up to $6 billion in federal support for commercial-scale demonstration projects that will curb CO2 from heavy industrial sectors. That program includes up to $500 million each for two new “direct reduced iron” plants that run on clean hydrogen instead of coal or fossil gas.
The $28 million initiative is funded by ARPA-E’s appropriations from Congress, through the Revolutionizing Ore to Steel to Impact Emissions (ROSIE) initiative while the much larger program announced earlier is funded by the Inflation Reduction Act and Bipartisan Infrastructure Law.
Globally, steel production generates as much as 9 percent of human-caused CO2 emissions every year — more than any other heavy industry.
About 70 percent of those emissions come from the ironmaking process alone. Existing blast furnaces use purified coal (or “coke”) and limestone to turn iron ore into molten iron at extremely high temperatures. A separate facility then turns iron into high-strength steel, which goes on to become car parts, structural beams, kitchen appliances, and much more.
ARPA-E said the 13 companies, universities -- including the University of Utah through and research institutions selected for award negotiations are primarily targeting those blast-furnace emissions. The U's award, amounting to $3,479,082, will advance a hydrogen-reduction melt-less steelmaking technology. The proposed process has the potential to drastically reduce energy consumption by eliminating several high-energy steps in traditional iron and steelmaking and is conducted at substantially lower temperatures than conventional methods. This approach is projected to decrease energy use by at least 50% in the production of steel mill products and up to 90% in creating near-net-shape steel components.
Pei Sun, Research Associate Professor in Fang's Powder Metallurgy Research lab is principal investigator of the funded project.
Read more about this story at Canary Media.