secret weapon in the race to mine more minerals
August 5, 2025
Above: Earth AI uses software and proprietary drilling hardware to find, verify, and sell multi-billion-dollar mineral projects. Credit: Earth AI; Alyssa Powell/BI
The US is scrambling to reduce its reliance on foreign sources of critical minerals.
The raw materials are essential inputs for modern technology. Smartphones, 5G networks, and military weapons like fighter jets are built using these materials, and they continue to be used to spur innovation. Lithium powers electric vehicle batteries, copper keeps data centers running, and silicon forms the foundation of semiconductors.
Demand is rising fast, with the global critical minerals market projected to reach nearly $500 billion by 2030, said Kings Research, a market research firm. Yet the US still relies heavily on imports. As of 2024, the country imported 100% of 12 out of 50 designated critical minerals, including graphite, manganese, and gallium, according to the United States Geological Survey, many of which come from China.
Now, under the second Trump presidency, the US is pushing to reestablish its dominance in mineral production. The administration has made domestic manufacturing a national priority, issuing an executive order to boost mining on American soil and imposing 50% tariffs on imported metals like steel and aluminum.
Rebuilding domestic mineral supply could strengthen the economy and improve national security. But it could also lead to supply gaps, potentially driving up the cost of materials that power innovation.
To prevent bottlenecks, startups and legacy tech companies are turning to artificial intelligence. Their AI tools promise to speed up mineral discovery and reduce supply chain risks in a volatile geopolitical climate.
But in a highly regulated industry where progress is slow, some experts question whether AI can deliver on its promises.
Startups are racing to reshape mineral exploration
Startups are betting on AI to discover new mineral deposits — and some are seeing early results.
Earth AI uses predictive software and proprietary drilling hardware to find, verify, and sell multi-billion-dollar mineral projects. Its algorithms are trained on decades of historical data from Australia, including past successes and failures of mineral discovery, to pinpoint hydrothermal systems: heated, mineral-rich waters likely to hold valuable deposits.
After identifying a promising site, the company drills using its own rigs and analyzes rock samples to confirm the presence of metal. Once proven, the site is sold to larger mining firms.
Earth AI said it has a success rate of 75% — far above the industry average of less than 1%. Over the last 12 months, the company said it has already made three discoveries in Australia, one of which is indium, a rare metal used in touchscreens and semiconductors for AI hardware. It's also discovering untapped reserves rich with minerals. In late July, Earth AI's software identified a massive underground trove of nickel and palladium in the east coast of Australia the company will drill.
By using AI, Earth AI told Business Insider it can cut mineral discovery timelines from years to months.
"We think that we can create the most value by drilling into the ground, proving that 'Yes, there are chemical concentrations of metal there,'" said Monte Hackett, CFO of Earth AI.
Terra AI is also betting that AI can speed up the industry's slow discovery process.
"Despite decades of investment in sensors and data, we're doing worse every year," said John Mern, cofounder and CEO of Terra AI. "The amount of metal added to the global supply this year is 90% lower than it was in 1990."
Terra's software uses AI to ingest layers of geological data — like magnetic field readings and seismic activity — used to generate thousands of underground maps to identify the most promising places to drill.
Mern said its AI-first approach is already being piloted on rare earth projects in the US and by mining companies across the Americas, Africa, and Europe. He added that Terra's platform could cut the 17-year average mine development timeline in half.
Investors see AI applications in mining as a major opportunity. Founders Factory, a UK-based venture firm, recently partnered with mining giant Rio Tinto to launch an accelerator backing 12 startups a year — including Terra AI.
Jack Kennedy, an investor at Founders Factory, sees mining as a $2 trillion industry that's been "untouched" by tech innovation. He compares mining to a "waste management business," where tons of earth are moved to extract small amounts of metal.
"AI is essentially a way to try and process tons of different data points to make efficiencies," Kennedy told BI. Doing so, he added, translates to reductions in waste, costs, and environmental impact.
Legacy players use AI to secure the supply chain
Legacy firms are also getting in on the action.
Exiger, a supply chain management software provider, helps governments and Fortune 500 companies track and secure critical mineral supply chains. Its AI model breaks down products into digital twins — detailed virtual versions that map the materials inside — then traces the material composition of the products using a database of 10 billion transaction records.
The database includes commercial datasets purchased from custom brokers and invoice processes, financial data, engineering specifications, build-to-print drawings, material declarations, and manufacturing process documents.
Using AI to assess a company's supply chain gives clients visibility into the vulnerabilities within their mineral supply chains, like where they may be over-reliant on certain countries and geopolitical risks. In turn, clients can make informed decisions when adjusting their mineral supply chain strategy.
In one case, Exiger identified how to extract germanium — a rare earth mineral used in fiber optics and chips — from coal ash and smelter waste in the US, potentially reducing foreign dependence.
"When China restricted exports on rare earths, it exposed customers to price volatility and geopolitical uncertainty," Brandon Daniels, CEO of Exiger, told BI. "Our platform helps clients navigate that risk with a level of precision previously unattainable."
The limitations of AI
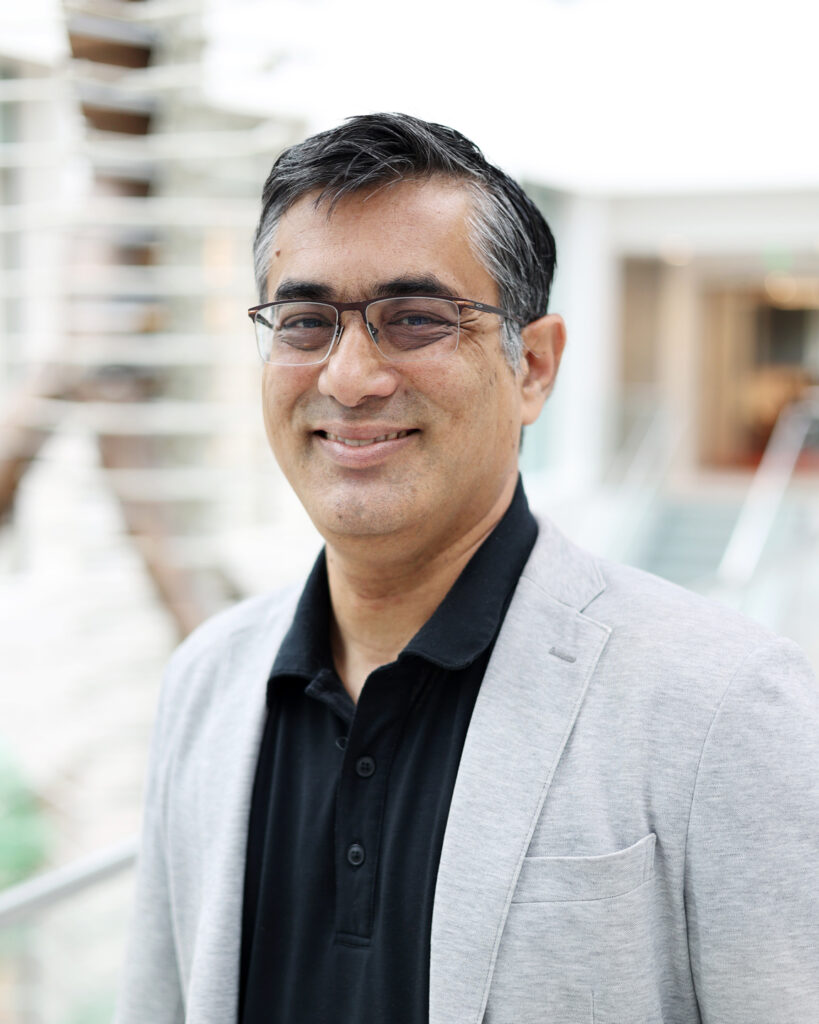
Rajive Ganguli
Still, AI isn't a magic solution.
Rajive Ganguli, the Malcolm McKinnon Professor of Mining Engineering at the University of Utah with decades of experience applying AI in the field, said the technology is only as good as the data it's trained on. High-quality, hard data — like drill hole information and physical samples — is often scarce, expensive, and difficult to obtain. [He spoke on behalf of the Society for Mining, Metallurgy & Exploration which represents the entire North American manufacturing industry.]
"AI on bad numbers does not result in good answers," Ganguli told BI. He also points out that many "AI discoveries" happen in areas already known to geologists. The technology, he said, doesn't work as well in unexplored, data-poor regions.
Additionally, the startups that spoke to BI said that the mining industry remains skeptical about embracing new technologies, making the adoption of AI in the critical mineral discovery process an uphill battle.
That said, Ganguli believes the biggest obstacles to scaling up mineral production aren't technological, but systemic. In the US, companies often wait 10 to 15 years to get permits approved.
Even though the Trump administration is making moves to fast-track permitting, the process continues to remain bottlenecked in the near term. Despite early talks with US clients, Earth AI hasn't begun exploration in the country due to delays that can drag on for years.
Experts agree that AI won't replace humans. Geologists and engineers are still essential for interpreting AI outputs and making final decisions about where to drill.
"This isn't a lab problem," Ganguli said regarding mineral discovery, adding that "domain experts" are crucial to understanding how the machines operate, what the data means, and how the site actually works.
Even so, companies believe AI can play a key role in strengthening the US mineral supply chain.
But even with the best tools, the US is unlikely to do it alone.
"The reality is, the majority of our supply chain is going to come from beyond our borders," Terra AI CEO Mern said. "We need responsible international partners to secure it."
by Aaron Mok
This story was first published August 4, 2025 in Business Insider.